Tino Fuhrmann the head of VW’s MEB project describes here the concept and design of the Modular Electric Drive Matrix, or MEB, platform
The last model with a combustion engine left the Volkswagen assembly line on June 26th at the Zwickau car factory. The seventh generation Golf R Estate with 2.0-litre petrol engine in Oryx White Pearl Effect was produced for a customer in Germany. From now on, only electric models of Volkswagen including the sister brands Audi and Seat will be produced in Zwickau. The leap into the modern automobile age has been a long one: since 1904, cars with combustion engines have been built in Zwickau, including Horch models, and in GDR times the Trabant came off the assembly line. In May 1990, Volkswagen started production at its plant in western Saxony. Over the course of the past 30 years, exactly 6,049,207 Volkswagen cars of the models Polo, Golf, Golf Estate, Passat Saloon and Passat Variant have been produced in Zwickau.
With a step-by-step transformation of the Zwickau plant, Volkswagen is switching a large car factory completely to electric mobility. which amounts to an investment of around 1.2 billion euros. In the final expansion stage from 2021, six MEB models will be built for three Group brands
. All 8,000 employees will be prepared for production of electric cars and for handling high-voltage systems as part of various training measures. The Zwickau team will complete around 20,500 days of training by the end of 2020. The ID.3 is the first vehicle based on the modular electric toolkit (MEB) from Volkswagen. The platform was developed specifically for electric cars and optimally exploits the possibilities offered by electric mobility. The market launch of the ID.3 1st Editionwill take place almost simultaneously throughout Europe in September 2020
Tino Fuhrmann the head of VW’s MEB project describes here the concept and design of the Modular Electric Drive Matrix, or MEB, platform
Without compromises
The new ID.3 will be the first model based on the modular electric drive matrix to be released onto the world market.
The MEB is the technical element that will link all future models in the ID. family: a platform specifically developed for purely electric vehicles. The components in the electric drive system and the package are therefore consistently interlinked. Offering a range on the level of today’s petrol-driven vehicles and available for the same price as a diesel car. The new ID.3 will be the first model based on the modular electric drive matrix to be released onto the world market, it also has the potential to facilitate the breakthrough of environmentally friendly electric mobility and usher in a new era of electric drive systems.
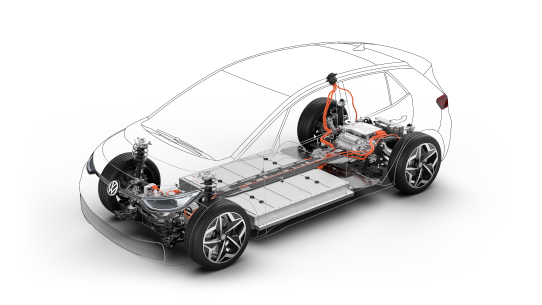
Revolutionary wheelbase, small overhangs
This enables Volkswagen to use the design specifications of the MEB to enhance the range, space, versatility, comfort and dynamics of models. These benefits will result in an entirely new form of mobility for drivers and passengers. The fact is that the interior dimensions and versatility of the ID.3 will exceed all current limits in its class. Just as revolutionary is the ratio of the extremely large wheelbases to the overall length, and the resulting short overhangs. This is possible because there is no need for a combustion engine in the front, and the axles can thus be transferred far toward the outside.
All components of the MEB drive matrix in detail
The zero-emission drive in the ID.3 primarily consists of an electric motor integrated into the rear axle together with power electronics and a gearbox, a high-voltage flat battery installed in the vehicle floor to save space and auxiliary powertrains integrated into the front end of the vehicle. The power electronics are effectively a link that controls the flow of high voltage energy between the motor and the battery.
The power electronics convert the direct current (DC) stored in the battery into alternating current (AC). Meanwhile, a DC/DC converter supplies the onboard electronics with 12 V of power. The 1-speed gearbox transfers the power from the motor to the rear axle. The motor, power electronics and gearbox form a single, compact unit.
The electric motor of the ID.3 has a power output of up to 110 kW / 150 PS. Electric drive motors offering either more or less power may be considered for the 2020 series version. In parallel to this, the idea is to be able to configure the ID.3 using different sizes of battery. This will enable the drive to be precisely attuned to how that specific car is to be used – as is standard for petrol and diesel engines. The battery’s modular layout allows scalable ranges from about 330 up to more than 550 kilometres (WLTP/Worldwide Harmonized Light Vehicles Test Procedure).
Ideal weight distribution
The battery is the decisive factor when it comes to the ID.3’s range. It is installed in the underbody, which saves space and significantly lowers the centre of gravity. The location of the battery in the centre of the vehicle results in optimal weight distribution of close to 50:50. The low centre of gravity and the balanced weight distribution lead to a driving behaviour that is dynamic as well as balanced.
Update-compatible hardware and software
The MEB will enable new assistance, comfort, infotainment, control and display systems to be integrated into vehicles across the board. The ID.3 features an AR (augmented reality) head-up display which projects information such as visual cues from the navigation system into the virtual space in front of the vehicle. Without the new platform, this technology would not be able to be integrated. To control the huge range of features on board the ID. models, Volkswagen has designed the completely new end-to-end electronics architecture, called E3, as well as a new operating system, called vw.OS (OS = operating system).
ID. family is always online
The models in the ID. family are always online and can access a range of information and services, some of which are entirely new. Volkswagen is therefore set to transform from a pure vehicle manufacturer into a mobility provider of vehicles and services characterised by extensive digitalisation. During this transformation process, the focus will be on electric mobility, connectivity (linking the vehicles with the users and the internet) and – from 2025 onwards – automated driving.
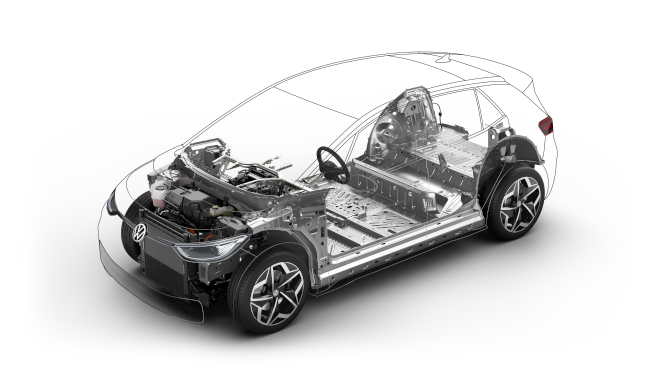
One chassis, many body versions
The range of MEB models will be just as large as the current crop of MQB vehicles. Other Group brands (Skoda, Seat, Audi) belonging to Volkswagen AG will also take advantage of the MEB.
What are the main materials, in the construction of the platform and which firms did you cooperate with in the construction?
Like the MQB models also the MEB family is mainly build of different steel alloyings including high tensile steels. The MEB contains some innovative measures. For example, aluminium rocker panels and a battery housing made of aluminium. Additionally, a seat lower cross-rail made from ultra-high tensile steel, thin high tensile door panels and a plastic rear gate.
Can the platform be customised for different applications?
Yes. The platform can carry different vehicle types. From compact hatches to SUVs, sedans and even Vans…
How many units do you hope to build in the next decade?
Our plan is to offer an all-electric vehicle in every segment with high demand. So, we will aim to sell up to 1,5 million electric cars yearly from 2025 onwards.
This is the most ambitious mobility plan in history. We’re uniquely positioned by our history, volume, reach, resources and technical capability to take E-Mobility mainstream.”
CUT COTS OF THE FLEET WITH OUR AUDIT PROGRAM
The audit is a key tool to know the overall status and provide the analysis, the assessment, the advice, the suggestions and the actions to take in order to cut costs and increase the efficiency and efficacy of the fleet. We propose the following fleet management audit.