As the demand for hybrid and electric vehicles continues to grow, a new generation of efficient, high-performing, reliable and environmentally-responsible electric motors is on the horizon. Axalta headquartered in Basel, Switzerland is a leading global supplier of liquid and powder coatings with over 70 years of experience as an international leader in the manufacture of high-quality insulation materials. Thanks to its leading position at the forefront of technological innovation, the company has developed technologies that enable the design of new, smaller motors with higher output and increased driving ranges.
Dr Christoph Lomoschitz, Axalta’s Global Product Manager for its Energy Solutions business says “Working in close collaboration with our customers, we thoroughly understand the needs of automotive component manufacturers, and we are always monitoring trends to anticipate how the industry’s needs will evolve. Today, we are already working on solutions for future requirements, and by doing so, we are helping to shape the next generation of electric motors” We are a leading global company focused solely on coatings and providing customers with innovative, colourful, beautiful and sustainable solutions. From light OEM vehicles, commercial vehicles and refinish applications to electric motors, buildings and pipelines, our coatings are designed to prevent corrosion, increase productivity and enable the materials we coat to last longer” he continues.
Innovative designs
New and improved electric motor designs have two primary objectives – increased power and reduced size. To achieve these, four distinct insulating product types come into play – electrical steel coatings, wire enamels, impregnating resins and casting compounds. Each of these addresses specific challenges to support the build of present and future new energy vehicles (NEVs).
The other important challenge when redesigning motors and their constituent parts is the facilitation of mass production, which must be taken into account in the initial design stage of the resin. “Our products are developed in such a way that curing times as well as coating and impregnating times are reduced to the lowest possible level, cutting the cycle time for each unit produced” explains Dr Lomoschitz. .
Drilling down
Electrically insulating liquids can be found in the four main usages in electric motors, each of which has its own issues and solutions.
The core
The metal core of a motor is usually made up of thin layers of pierced and punched sheets to limit the negative effect of eddy currents. Even when these are covered with an electrical steel coating, a weak spot can be caused during interlinkage by welding, screwing or interlocking. These conventional connections also form an electrically-conductive bridge which can reduce the efficiency of a motor, as the metallic connections form short circuits which cause an increase in eddy current losses.
A solution to these issues is to glue the sheets together instead, by using insulating bonding varnishes. Gluing offers the advantage of also creating a stiffer core. Welds, interlockings, clamps, rivets and screws only offer a local connection between the single laminations, whereas glue holds the entire laminate stack together. Consequently, this form of bonding also reduces the noise caused by the inevitable vibrations of the motor during operation, which is another advantage.
The conductor
Due to its excellent electrical conductivity and its availability, standard round magnet wires are usually made of copper. While these are still state-of-the-art for most current motors, new designs such as those with rectangular-shaped cross sections are gaining more traction. However, these designs bring adherence, flexibility and appearance issues to the wire enamel. To reduce weight and centrifugal forces, aluminium is being considered as an alternative as it has similar conducting properties to copper, but at a much lower weight and cost. However, the enamelling process for aluminium is more demanding.
Higher voltages, silicon carbide (SiC) technology and inverters can create conditions that initiate partial discharges which quickly dissipate a standard varnish. Insulating materials can be affected by either thermal degradation or electric degradation, or both depending on the operating condition of the motor. Below operating voltages of 600 to 800 Volts, thermal degradation is predominant and occurs at long lasting exposure to high temperatures.
Depending on the material, thermally induced degradation may take place from 120oC. In automotive applications, insulating materials that can withstand at least 180oC in continuous operation are already commonly used. With the latest generations of NEVs, the operating voltage of electric motors has risen to a level of 600 to 800 Volts and is expected to increase even further. Additionally, these motors are usually inverter driven (DC to AC current), so that the peak-to-peak voltage could be in excess of 1kV.
Under these conditions partial discharges may occur, which are the major cause for electric degradation. Partial discharges are best described as small sparks constantly striking in the same spot, leading to local destruction of the insulating material. These partial discharges steadily damage the impregnating resin, thus significantly reducing the protection it provides to the wire enamel, which is consequently also exposed to partial discharge. With the primary insulation degrading, electric failures occur.
“With Voltatex® 7740 and Voltatex 8534, we have introduced an enamelling that significantly reduces the impact of partial discharge and significantly extends the durability as well as the reliability of electric motors. Both of these wire enamels are part of Axalta´s Voltron® System, which has the first patented dielectric based on nanotechnology that enhances corona discharge resistance. The use of nanoparticles is the major mechanism in reducing electrical ageing” says Frank Saborowski
“It is crucial that the wire enamel is adapted for the impregnating resin that later covers the entire device to obtain the best wetting and compatibility. This has been achieved by specifically engineering the surface of the wire enamels in Axalta´s Voltron range” Saborowski continues.
The cover
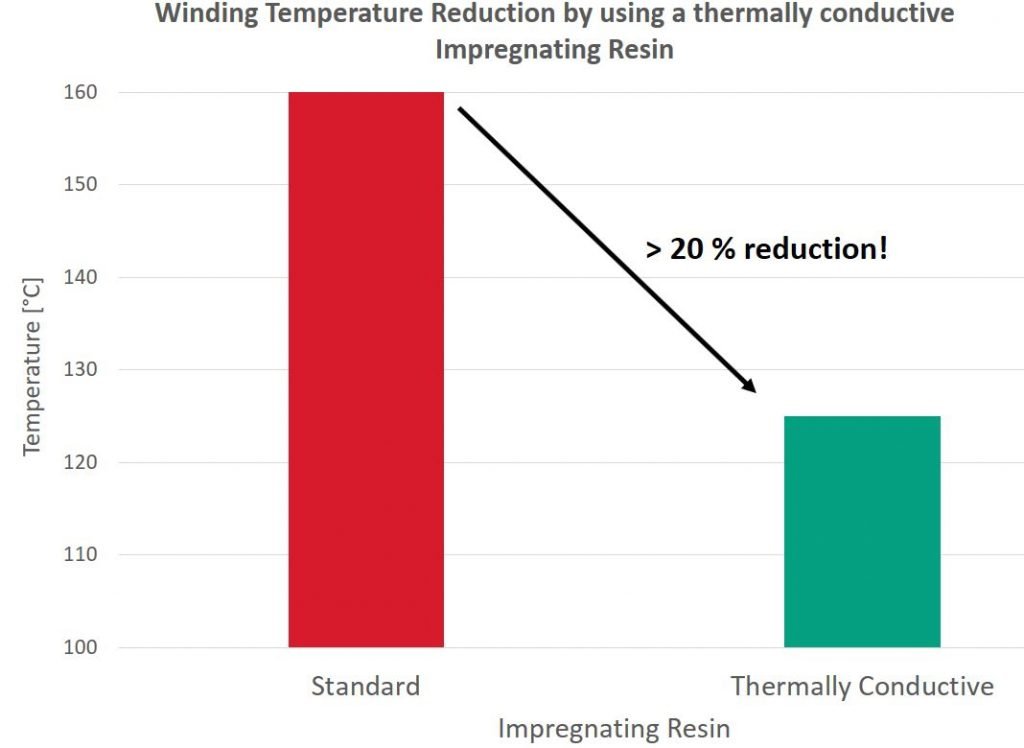
More output and higher efficiency are the usual goals when designing modern motors; today, the entire design process is focused on achieving these results. One solution is to increase the voltage at which the motor is operated, another is to replace the random wound round wire design with a rectangular hair pin design. A round wire design leaves more void space, whereas the use of rectangular wires enables the elimination of void spaces to a major extent. Higher copper fill factors in the slots are achieved through a tighter-packed winding. This has numerous implications in the development and application of impregnating resins.
Void spaces have to be filled by the impregnating resin for a number of reasons:
- To dissipate heat from the motor by increasing the system’s thermal conductivity.
- To reduce partial discharge and its deteriorating effects, as air may be easily ionized, thus leading to small sparks.
- To increase the mechanical stability of the unit by preventing the conductor from moving or vibrating.
The penetration of the impregnating resin is predominantly determined by the resin’s viscosity and the system’s surface tension, as well as its ability to flow, and the dimensions of the void spaces. The rectangular conductors offer the benefit of getting more copper into the motor, which increases its efficiency. However, while the void spaces left are smaller, the development of the impregnating resin and the application process become more complex in order to achieve the same penetration that is reached with round wires.
Impregnation is about heat dissipation and structure stabilisation to make it more durable. Axalta has recently launched Voltatex 4224 – a ground-breaking impregnating resin that meets the major challenges of modern electric motor designs, as it provides significantly increased thermal conductivity and a much higher resistance against partial discharge. Most thermally conductive materials on the market have high viscosities that require very demanding application processes to force the resin into the void spaces. Because of its very low viscosity and optimised flow characteristic, Voltatex 4224 very effectively reduces operating temperatures without sacrificing processability and can be used in standard impregnating processes. To achieve this, Axalta´s Research & Development had to create a resin system specifically designed for these tasks and incorporate the improved thermal conductivity into it. The improved heat transfer from the copper winding to the steel core causes less thermal stress in the motors’ components.
The casting
The platform concepts of future NEVs require the power train to take up as little space as possible. To keep it small, manufacturers aim to house all its components tightly together. For the motor to run efficiently, a forced cooling is favoured which uses either water, oils or other cooling liquids to dissipate heat. These must not come into contact with the other drive train components. For some uses, particularly in the case of very high performing motors, casting resins can be beneficial over impregnating resins. Although this group of secondary insulating materials is more demanding by way of their application, casting resins can offer outstanding thermal conductivity and very high stability.
Axalta has created a number of casting resins in the Voltacast range. These are polyurethane or epoxy-based two-component systems, consisting of a resin and the corresponding hardener. Depending on the composition the polyaddition reaction during chemically curing results in the production of different grades of a duroplastic material, each with system-specific end properties. These casting resins are designed to protect all non-moving electrical devices, such as transformers and ballasts, from the destructive influence of vibrations, pollution, liquids and thermal and mechanical stress.
Looking to the future
Non-governmental as well as official initiatives around the globe are striving for increased future usage of NEVs over conventional internal combustion engine technologies. To meet the associated challenges, innovation and new ways to approach existing problems are key, as lighter, cleaner and more efficient hybrid and full electric vehicles must be developed. The existing technological boundaries must be broken.
“Our company is ideally positioned to introduce ground-breaking technologies to this field, thanks to its excellent track record as a long-standing supplier to leading automotive OEMs and Tier 1 suppliers. For Axalta’s Energy Solutions business, the future is already here” concludes Dr. Lomoschitz .
By , and Frank Saborowski, Axalta’s Wire Enamels Product Manager for its Energy Solutions business
CUT COTS OF THE FLEET WITH OUR AUDIT PROGRAM
The audit is a key tool to know the overall status and provide the analysis, the assessment, the advice, the suggestions and the actions to take in order to cut costs and increase the efficiency and efficacy of the fleet. We propose the following fleet management audit.