Fleets share updates they have made to everyday operations.
In early 2020, as COVID-19 began spreading rapidly across the U.S., the Electric Utility Fleet Managers Conference developed the EUFMC Education Connection to provide valuable information on fleet operations and shop practices that were implemented as a result of the pandemic.
Among the topics discussed by fleet executives were how to prioritize work with operations scaled to essential activities only, connecting with shop employees when working remotely, and how to properly sanitize vehicles and what products were approved to do so. Also on the list were how single driver per vehicle policies were leading to rentals or reallocating assets as well as reforecasting budgets to address new allocations.
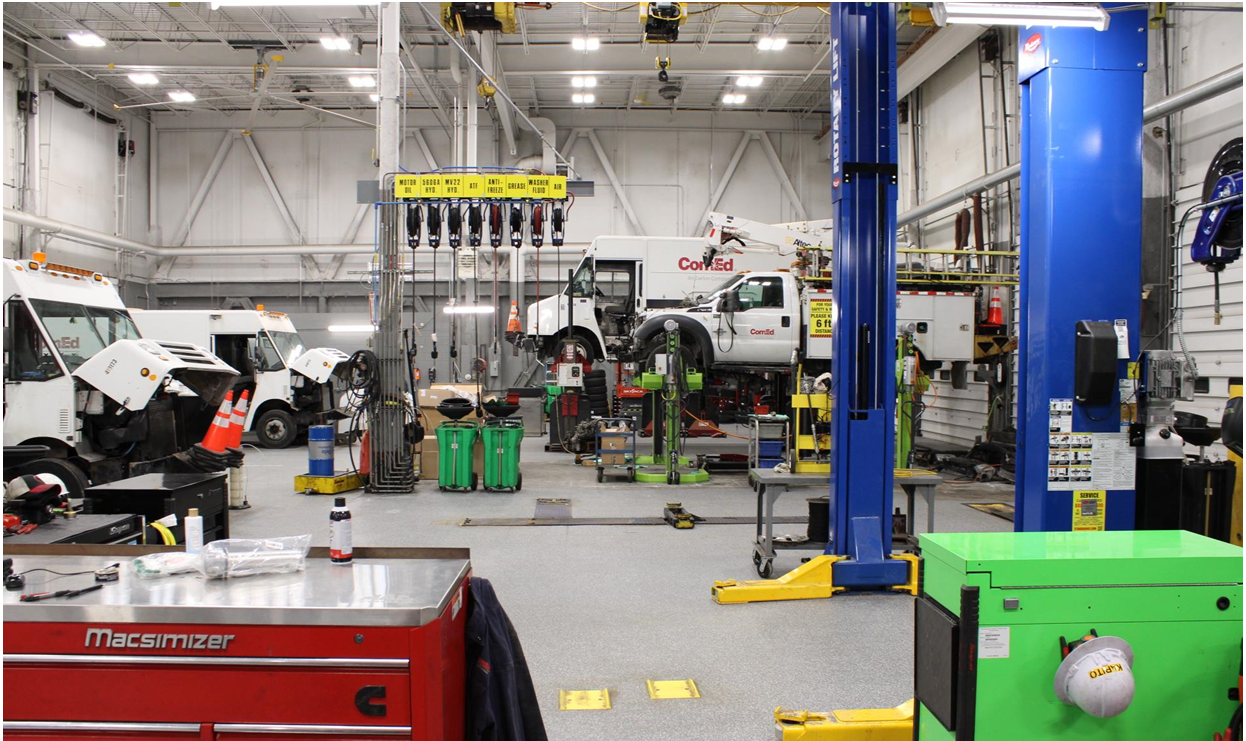
The group also covered what fleet managers saw as programs and procedures that are necessary for returning fleet staff to work safely. At that time, early preparations included planning to bring people back in stages but continuing to maintain social distancing by staggering shift start times and having gaps between shifts so areas such as locker rooms would not be crowded.
Recently, several EUFMC fleet representatives revisited those subjects and discussed which shop safety practices put in place during COVID-19 are still in effect, and the latest programs and procedures being used to return fleet staff to work safely. Looking ahead, they also commented on which shop safety practices they anticipate will continue to be in effect in a post COVID-19 world, and why they are necessary.
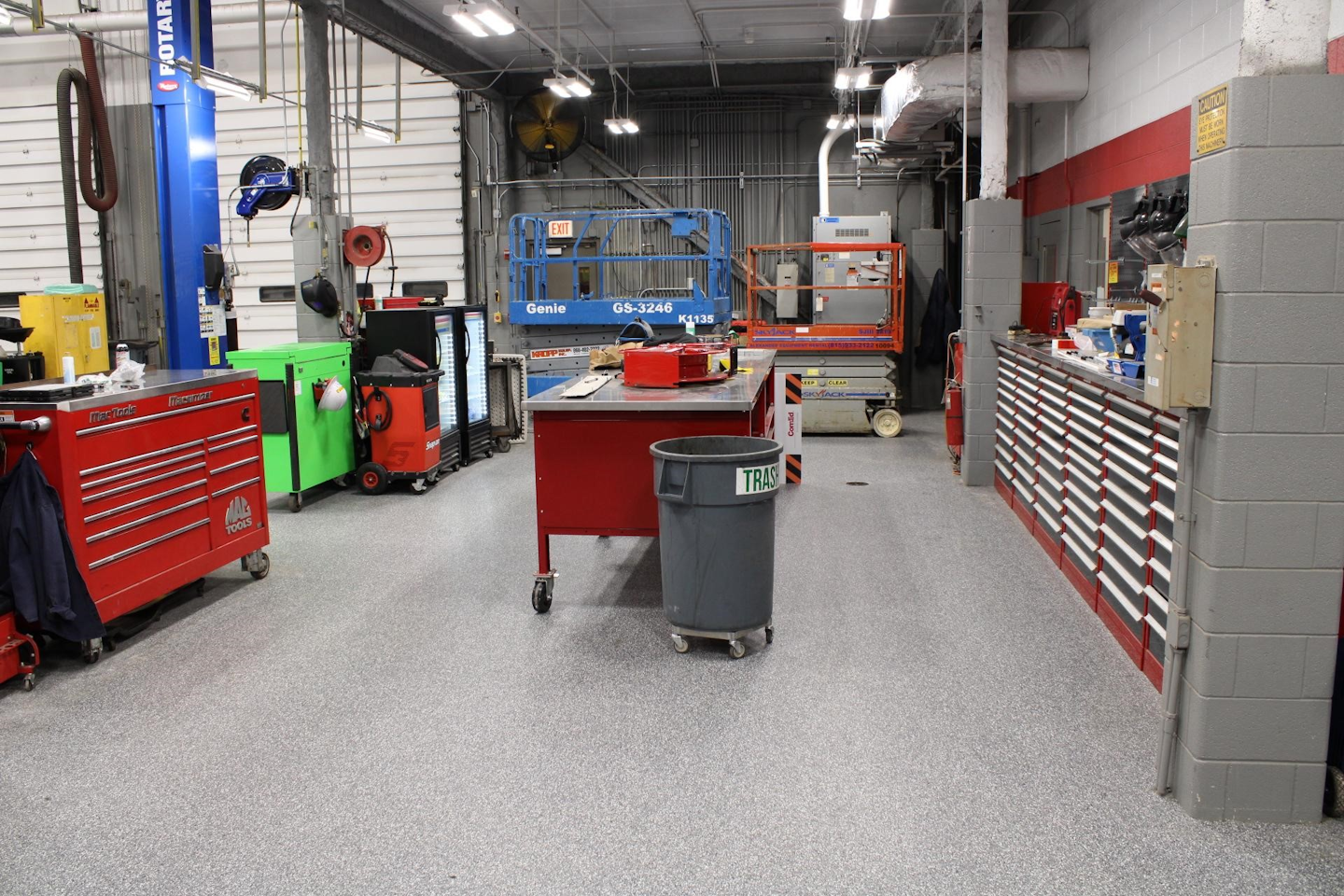
“We have shop operations running at full scale but staggered shifts starting at 5 and 6 AM and 1:30 and 2:30 PM,” said Mark Booker, fleet manager at Nashville Electric Service. “Our shop office entrance is limited to two fleet employees at a time, and we follow health department guidelines for social distancing and masks. At all shop entrances there are stand mounted stations with hand sanitizer, masks, and gloves, and we’ve made disinfecting wipes and bleach solutions available to address common touch points in shops and on vehicles. We also limit vendors on our property to properly masked parts delivery, service, and essential facility work personnel.
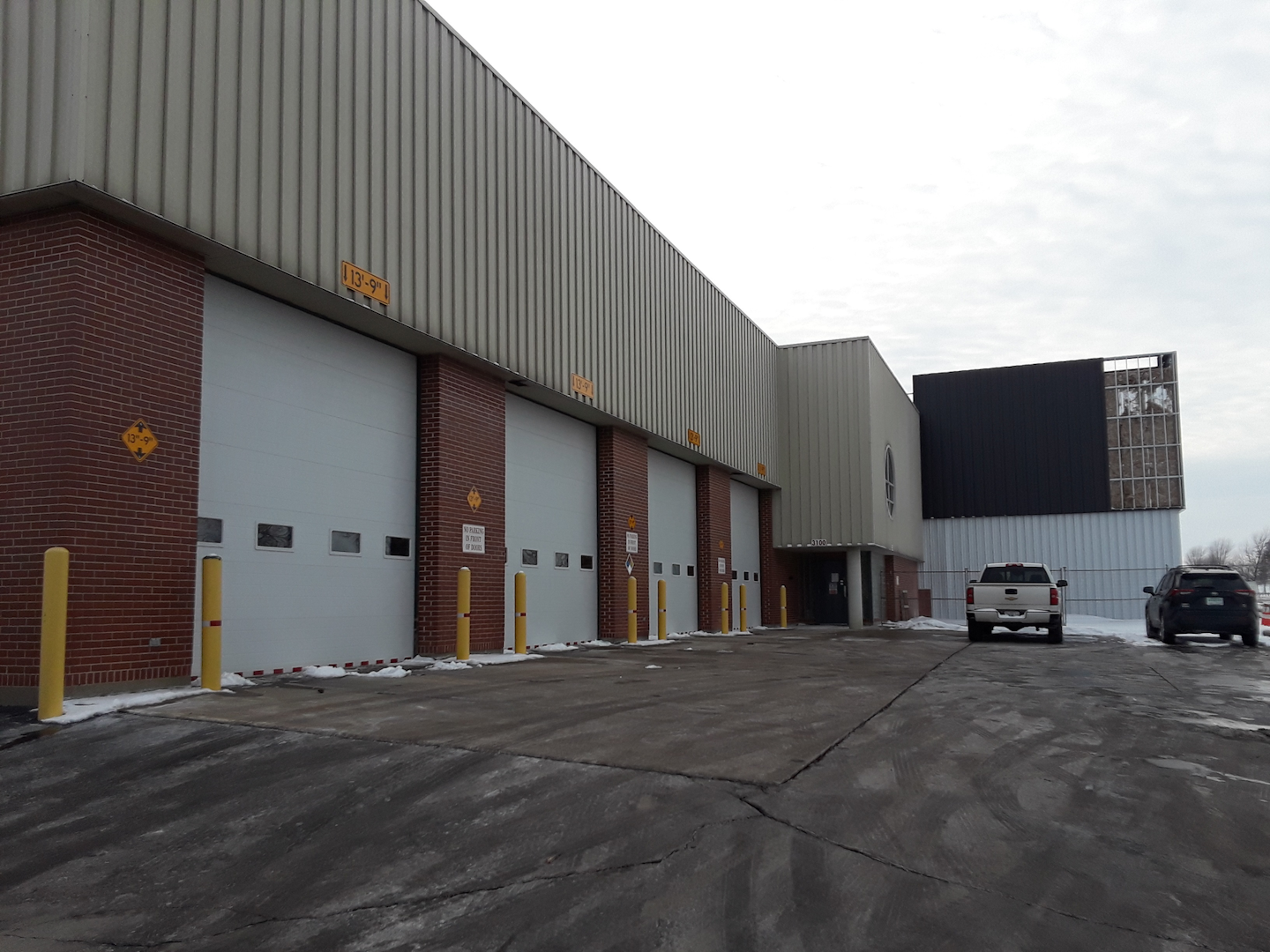
“In our shops, we’re also focusing on a continued effort to reduce shared diagnostic electronics to improve hygiene,” Booker continued. “Our practices also include putting vehicles and other areas exposed by direct contact out of service until they are disinfected the same or next day by a contractor. As we go forward, we will continue to have virtual meetings when it’s not necessary to gather in person, which also improves time management, and we will follow health department and company guidelines related to COVID-19 and reporting, as well as provide vaccine education.”
David Russell, manager of transportation at Liberty Utilities, reported that the fleet has no plans to discuss bringing all technicians back to the shop until after April of this year.
“For now, only one mechanic per shift reports to the shop while others take a service truck home and report to outlying storerooms,” he related.
“In addition, we’re monitoring individuals who enter a facility and all vehicles being worked on are sanitized with a handheld cordless sprayer before and after repairs,” Russell continued. “To ensure the safety of our employees as well, everyone follows glove, mask, and distancing safety protocols.”
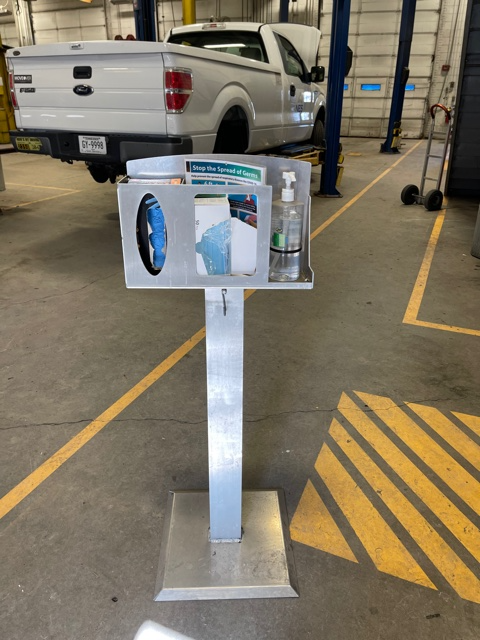
Mandatory masks, distancing, and staggered lunch breaks, handheld thermometers throughout facilities, and regular shop and vehicle sanitizing are practices that will remain in effect at ComEd, noted Joseph Moser III, manager fleet. In addition, all back office staff and managers are working remotely, and managers with responsibilities for employee engagement practice the 3 W’s – wear a mask, watch your distance, wash your hands – when visiting shops.
“We have a plan for returning to work based on vaccinations, decreases in positivity rates, and a revamped approach to being in the office,” Moser related. “While our shop staff will be on site, our back office teams will utilize a phased approach with a final objective of a permanent reduction in office time and taking advantage of remote capabilities.
“Our work has not been restricted, and even though we’ve had a complete shop staff on quarantine at times in some locations we have been resilient enough not to impact service levels for the fleet,” Moser added. “The pandemic has shown that working remotely has not affected our ability to perform and meet our objectives.”
Held annually in June in Williamsburg, Virginia, the Electric Utility Fleet Managers Conference will be a virtual event in 2021. For more information, visit eufmc.com.
By Seth Skydel
Source: https://www.fleetmaintenance.com