Con la nueva normativa europea de baterías, que pretende que éstas sean más duraderas, sostenibles y eficaces, podrían estar a punto de cambiar los estándares de las marcas en cuanto a diseño, fabricación y gestión del reciclaje del principal componente de sus coches eléctricos. Sobre todo, aquellas que han adoptado los diseños de batería estructural.
Y es que esta normativa no sólo estipula ‘un pasaporte digital’ o etiquetado obligatorio para las baterías de cualquier tipo de vehículo eléctrico (ya sean coches, camiones, autobuses, bicicletas o patinetes), sino que también pretende que se incluyan más materiales reutilizados en su composición y sean más fáciles de reciclar. Para esto, han de ser accesibles.
Cómo va a cambiar la forma de fabricar baterías para coche eléctricos
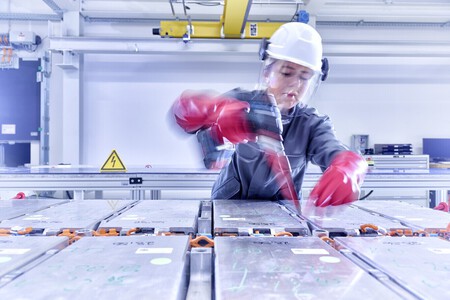
La nueva normativa de baterías de la UE, que lleva fraguándose desde 2020, pretende abarcar todo el ciclo de vida de una batería: desde la obtención de la materia prima para su fabricación hasta su reciclado al final de su vida útil. Y pese a que los eléctricos aún no acaban de despegar, de aquí a 2030, se prevé que haya 30 millones de estos vehículos en circulación por Europa.
En este contexto cabe destacar que, en los últimos años, muchos fabricantes han apostado por invertir en una mayor integración de sistemas en sus coches eléctricos, incluyendo baterías con diseños “cell-to-body” (célula-cuerpo) o “cell-to-chassis” (célula-chasis), que pueden ser más difíciles de desmontar o retirar. Ejemplo de ello son BYD, start-ups como Leapmotor o Tesla.
Pero con la adopción de la nueva normativa esta tendencia podría estar a punto de cambiar y, los fabricantes que querían que sus coches eléctricos tuvieran baterías estructurales, tendrían que dar un paso hacia atrás para poder ir nuevamente hacia adelante, si es que quieren vender sus vehículos eléctricos la próxima década en un mercado tan goloso como es el europeo.
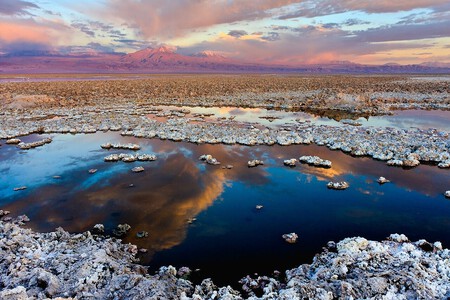
Para reducir el impacto de la fabricación inicial de las baterías, la norma exigirá mayor cantidad de material reciclado, y también fija objetivos sobre la cantidad de litio (50 % para 2027 y 80 % para 2031) y cobalto, cobre, plomo y níquel (90 % para 2027 y 95 % para 2031) que deben recuperarse de las baterías usadas una vez hayan llegado al final de su vida útil.
Facilitar la extracción de la batería del vehículo y su desmontaje en piezas podría ayudar a los recicladores a largo plazo, pues hemos de tener en cuenta que, sólo para cumplir con los planes de transición energética de los Veintisiete, Europa necesitará hasta 18 veces más litio del que usa actualmente en 2030 y de cara a 2050, casi 60 veces más.
En este sentido, un estudio de IDTechEx sobre el mercado del reciclaje de baterías estima que “en 2043 se tendrán que reciclar 23,8 millones de toneladas de baterías de iones de litio”.
La clave está en la estructura interna
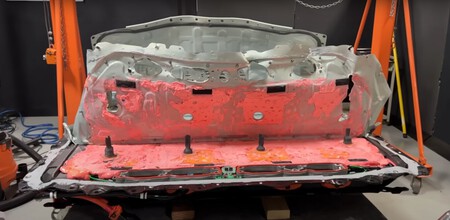
Baterías 4680 de Tesla
Cabe recordar que el diseño “célula a célula” implica que las baterías están compuestas por células individuales, lo que podría hacer que el desmontaje sea más sencillo. Sin embargo, este tipo de diseño a menudo hace un uso excesivo de adhesivos y espumas que dificultan el desmontaje y al final podría requerir reemplazar toda la batería en caso de falla.
Si los adhesivos o encapsulantes utilizados pudieran disolverse sin dañar las celdas, esto podría simplificar el reciclaje y ser un punto de diferenciación viable para los proveedores.
Por otro lado, el diseño “célula a chasis” implica que las células están unidas como un único módulo, lo que puede dificultar enormemente la extracción de la batería del vehículo y, por lo tanto, su reciclaje. Sin embargo, la normativa de la UE no dice nada sobre la estructura interna de la batería (estructura del módulo, separadores de celdas, etc.).
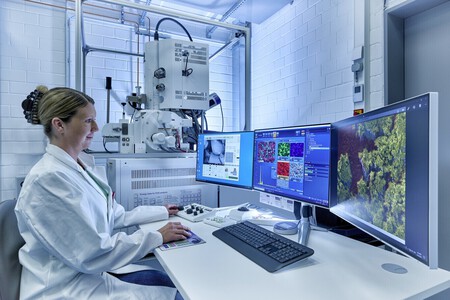
Asimismo, aparte del reciclaje, la normativa también contempla la posibilidad de darle una segunda vida a las baterías de los eléctricos por ejemplo como almacenamiento estacionario de energía.
En este caso, si el pack forma parte de la estructura del vehículo, aumentaría el tiempo de desmontaje, lo que encarecería el proceso de reutilización. Sin embargo, un diseño “célula a pack” podría reducir los tiempos de desmontaje y los costes de remanufacturación.
Así, con sus ventajas e inconvenientes, es probable que los diseños “célula a paquete” y “célula a chasis” continúen coexistiendo a corto plazo. Pero a medio y largo plazo, una vez que más baterías de vehículos eléctricos vayan llegando al final de su vida útil, las dificultades y el esfuerzo de reciclar grandes cantidades de baterías muy integradas podrían hacerse evidentes.
Sobre todo, a medida que los objetivos de recuperación de materiales críticos sean cada vez más estrictos, los diseñadores tendrán que redoblar esfuerzos.
Escrito por:
Fuente:: Motorpasión
Suscríbete a laNewsletter de gestión de flotas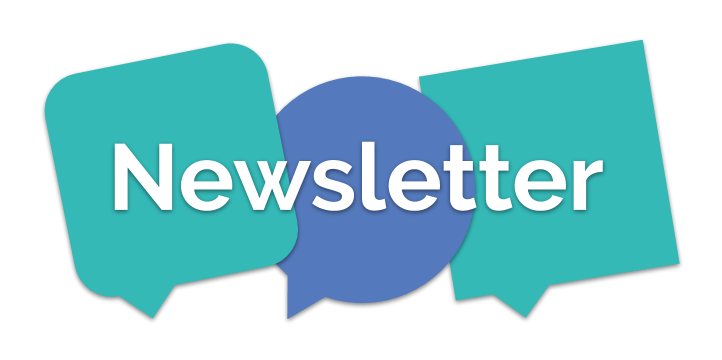
Curso ONLINE para la gestión de flotas de vehículos
Advanced Fleet Management Consulting, Webfleet Solutions, Optimatics, Mobileye, GantaBI, Unigis, Eccocar, y Alcoa Wheels organizan el “Curso para la Gestión de flotas de vehículos” con el fin de formar a los profesionales en gestión de flotas a tomar una visión global y conocer todas las actividades y factores clave involucrados en la gestión de una flota de vehículos.
El curso es único y presenta un enfoque innovador con los objetivos de reducir costes y optimizar la gestión de la flota.
info@advancedfleetmanagementconsulting.com
o
Rellena el siguiente formulario para recibir la información del curso y te puedas inscribir.